Implement scalable Advanced Process Control for optimal plant performance.
Advanced Process Control
When PID Control is Not the Optimal Solution
Sometimes PID control is not the optimal solution and applying advanced controls to your process would provide superior results. But without the right knowledge and tools, applying complex control strategies can be time-consuming and challenging.
MANTRA Software provides Advanced Process Control in a PC-based supervisory control system with a graphical programming environment for easy implementation and maintenance. Leveraging a suite of patented model-based control technologies and executing on your control network, MANTRA software runs control calculations in real time working with your existing DCS, PLC or plant-wide information system.
- ✔ Reduce control programming time by 50% or more
- ✔ Integrate with existing business and plant infrastructure
- ✔ Improve operations with no capital investment
- ✔ Improve safety and reduce risks
- ✔ Receive post-commissioning operator training
- ✔ Benefit from our extensive knowledge of major PLCs and DCS
ControlSoft engineers can help you design model-based controls within MANTRA software and also make modifications to your DCS/PLC control logic to reliably and safely implement advanced process control in your plant.
Save Time and Get Optimal Results
Graphical Programming Environment
Intuitively build basic and advanced control schemes in the MANTRA application developer. Simply create a block diagram within a project, and drag and drop objects onto the diagram, adding inputs, updating parameter types, and placing them in sequence to perform the necessary control functions to regulate and control your application process.
MANTRA Software – Application Developer Block Diagram
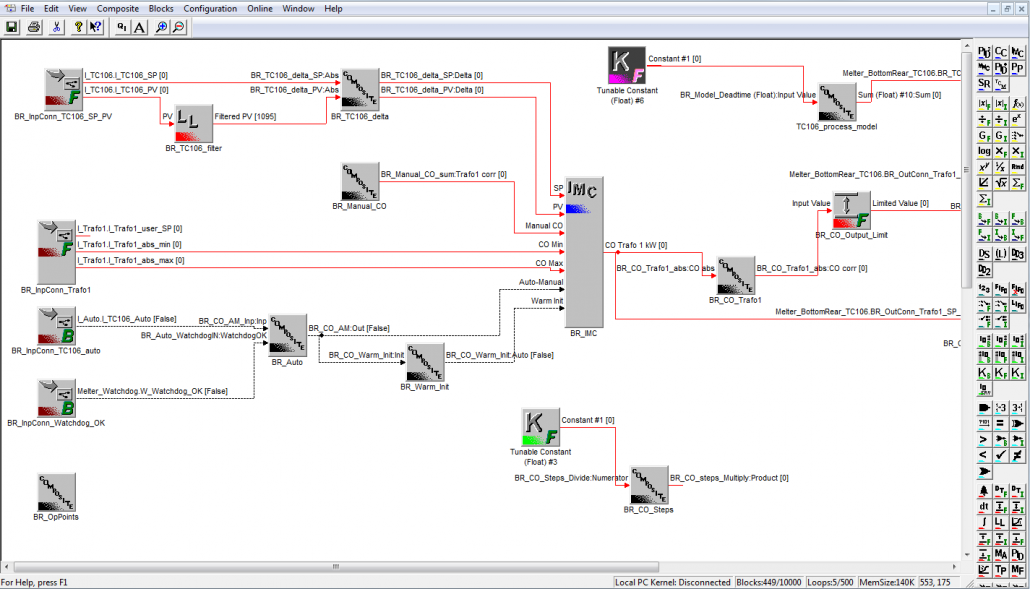
MANTRA software provides the ability to make changes to your project, without disrupting your operations. You can make incremental changes to your running project as needed, and update your project while avoiding costly shutdowns.
Patented Technology
Leverage ControlSoft’s patented control strategies for complex and difficult-to-control processes. Our suite of control technologies includes:
- Model-based auto-tuning
- Process loop monitoring and diagnostic methods
- Model-based multivariable control
Advanced Control Function Blocks
Work with a library of control algorithms that are packaged in easy-to-use function blocks. Each block is an object and can be manipulated graphically to add inputs, change parameter types (input to tunable or vice-versa), or even encapsulate several blocks in one.
Built into all the control blocks are advanced features such as feedforward, tracking, and alarming. Combining PID with special functions (like time proportional, position proportional, and lead-lag compensation) can help to easily develop complex process control schemes.
Industry Standard Connectivity
MANTRA software uses industry-standard OPC communications for reading live process data and periodically writing calculated optimal outputs and setpoint settings to your PLC/DCS system.
Your Challenges are Known to Us
The challenges you face occasionally are the things we deal with every day, in your industry and across a dozen others. Sample applications where MANTRA software has been used:
- Boiler Control
- Chemical Reactors
- Cooker Stations
- Dryers
- Extrusion
- Fermentation
- Scraped Surface Heat Exchangers
- Water Wastewater Treatment (Chlorination, Dechlorination)
Build Your Expertise in Advanced Control
Learn the advantages and disadvantages of different control strategies. Our modular courses cover:
- PID Controller Tuning
- Advanced Process Control Techniques
- Model-based Control
- Power Gen & Boiler Tuning
Offered virtually and in person, our hands-on training will give you the confidence to apply what you’ve learned for measurable results.