ControlSoft, Inc. is pleased to announce the release of INTUNE PID Loop Tuning Tools and INTUNE+ CLPM Software v7.0. INTUNE PID Tuning Tools includes robust auto-tuning and advisory adaptive-tuning tools that minimize the effort needed to optimally tune your PID controllers. INTUNE+ CLPM Software is a non-intrusive plant management and process control predictive maintenance tool that combines process control monitoring with powerful diagnostic and tuning features.
INTUNE v7.0 includes enhanced tuning formulas to improve PID terms for time-constant dominant non-integrating processes. Improvement is pronounced for slow dynamics.
Figure 1 – Adaptive Tuning
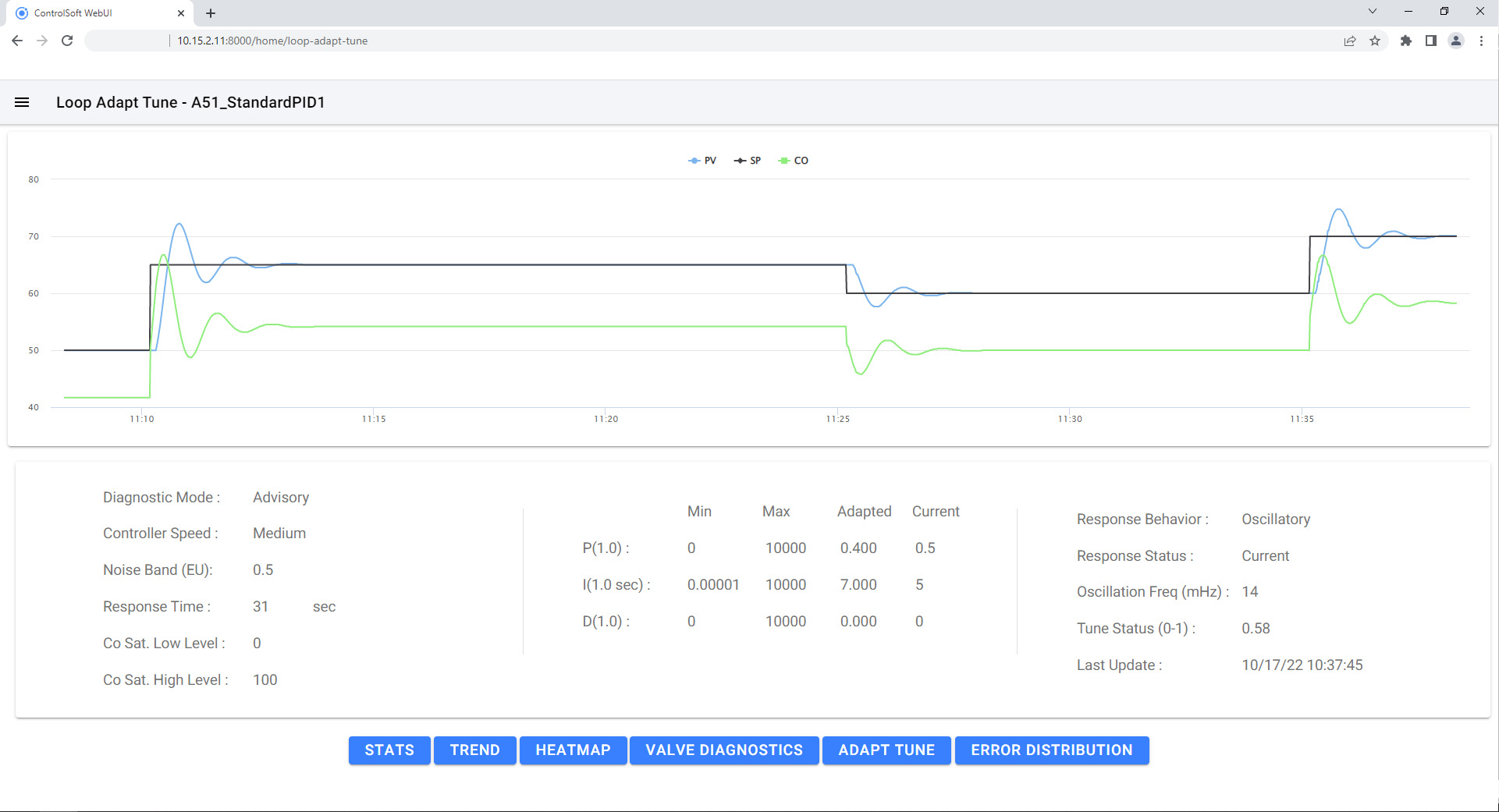
In addition, INTUNE v7.0 also includes the following updates:
- OSIsoft PI Data Driver that easily connects to a OSIsoft PI server to access data.
- OSIsoft PI Data Import that easily connect to PI AF SDK to access historical data in INTUNE’s DataTune plugin. You can map process datapoints to PI historical tags (PV, SP, CO, Mode).
- Server and Tag Browsers that can be integrated with other data drivers including OPC DA and OPC UA.
INTUNE+ CLPM v7.0 includes all the INTUNE v7.0 updates, as well as a new WebUI. You can connect this WebUI to an INTUNE+ CLPM project after it is completed and deployed for a clear and concise view of loop performance.
Figure 2 – INTUNE+ CLPM WebUI
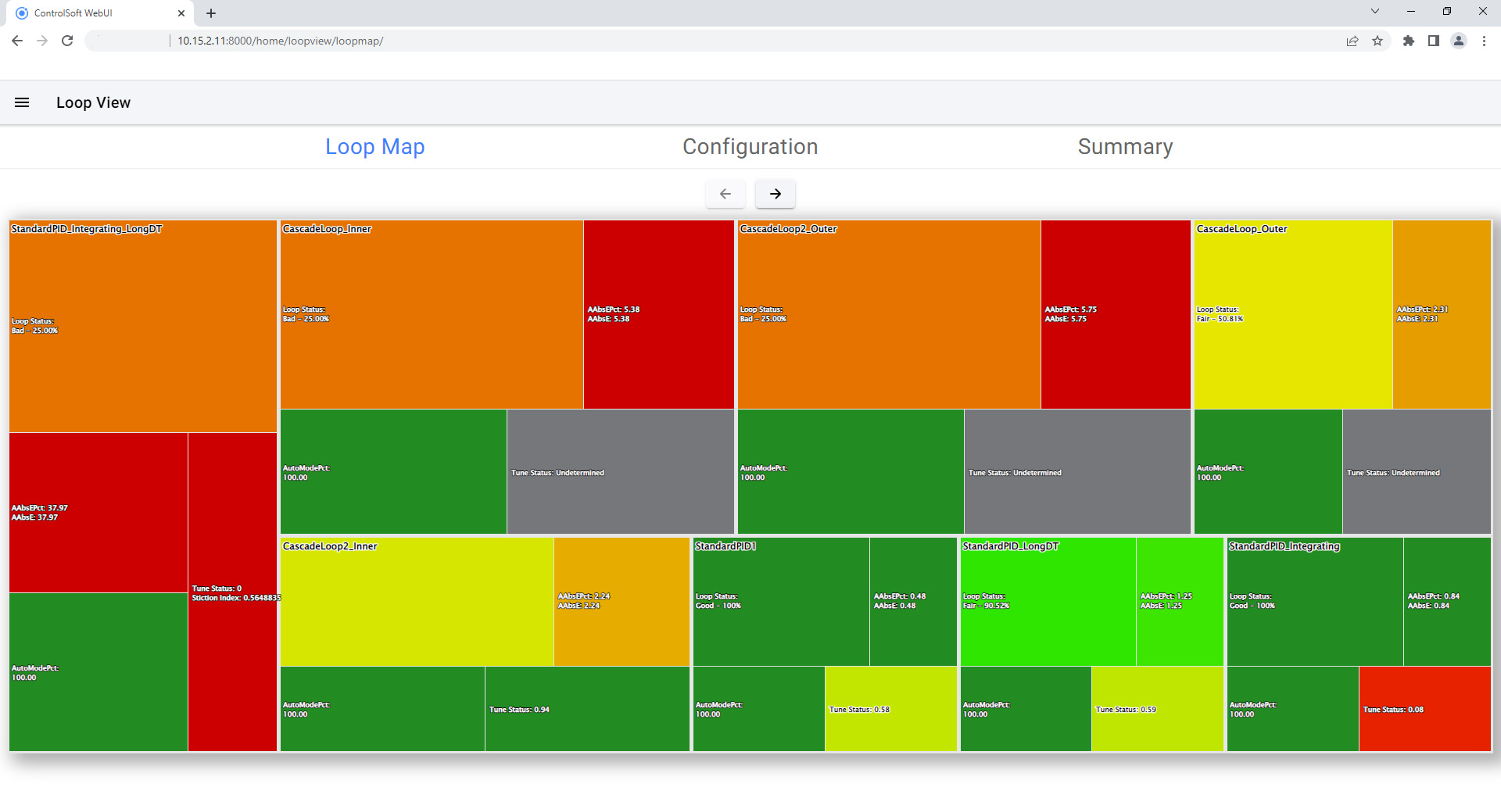
For detailed information, please see the INTUNE Software v7.0.0.2 Release Notes, publication MN112A-EN, included with the software download.
About ControlSoft
Since 1985, ControlSoft has been a global provider of platform-independent process control software and engineered solutions. Our products and services are sought by prominent companies in leading industries. By keeping a focus on improving plant availability, production efficiency, operational safety, and environmental compliance, we continue to deliver world-class control solutions for our customers.
INTUNE is a registered trademark of ControlSoft Inc.
Media Contact
Paul Botzman
pbotzman@controlsoftinc.com
phone 440-443-3900, ext. 101
Applying PID Control to Non-linear Processes
/in ArticlesMatt Petras, Alireza (Ali) HajiValizadeh
August 30, 2023
Control Engineering: https://www.controleng.com/articles/are-you-applying-a-pid-control-to-non-linear-processes-correctly/
Tuning Cascade Loops
/in ArticlesDerivative Tuning for PID Control
/in ArticlesMANTRA Software v5.6
/in Press ReleasesControlSoft is excited to announce the release of MANTRA Software v5.6 which includes the following user interface and tool enhancements:
features and usability enhancements.
For detailed information, please see the MANTRA Software v5.6.0.1 Release Notes, publication MN338A-EN, included with the software download.
For more help with advanced techniques for process control strategies beyond basic PID control, including cascade control, override control, gain scheduling, feedforward compensation, and model-based control, consider our Advanced Process Control Techniques training.
INTUNE PID Tuning Tools and INTUNE+ CLPM Software v7.0
/in Press ReleasesControlSoft, Inc. is pleased to announce the release of INTUNE PID Loop Tuning Tools and INTUNE+ CLPM Software v7.0. INTUNE PID Tuning Tools includes robust auto-tuning and advisory adaptive-tuning tools that minimize the effort needed to optimally tune your PID controllers. INTUNE+ CLPM Software is a non-intrusive plant management and process control predictive maintenance tool that combines process control monitoring with powerful diagnostic and tuning features.
INTUNE v7.0 includes enhanced tuning formulas to improve PID terms for time-constant dominant non-integrating processes. Improvement is pronounced for slow dynamics.
Figure 1 – Adaptive Tuning
In addition, INTUNE v7.0 also includes the following updates:
INTUNE+ CLPM v7.0 includes all the INTUNE v7.0 updates, as well as a new WebUI. You can connect this WebUI to an INTUNE+ CLPM project after it is completed and deployed for a clear and concise view of loop performance.
Figure 2 – INTUNE+ CLPM WebUI
For detailed information, please see the INTUNE Software v7.0.0.2 Release Notes, publication MN112A-EN, included with the software download.
About ControlSoft
Since 1985, ControlSoft has been a global provider of platform-independent process control software and engineered solutions. Our products and services are sought by prominent companies in leading industries. By keeping a focus on improving plant availability, production efficiency, operational safety, and environmental compliance, we continue to deliver world-class control solutions for our customers.
INTUNE is a registered trademark of ControlSoft Inc.
Media Contact
Paul Botzman
pbotzman@controlsoftinc.com
phone 440-443-3900, ext. 101
PID Loop Tuning Pocket Guide v7 Now Available
/in Press ReleasesWe’re excited to share a new version of the PID Loop Tuning Pocket Guide to help your team simplify processes so you can deliver your best. As fellow engineers, we know that properly tuned PID loops are crucial to enhancing your plant’s performance. That’s why we’ve thoughtfully redesigned this pocket guide based on your feedback.
This quick reference guide introduces your team to the process of manual PID tuning. It covers things like:
Download the guide today and learn how to efficiently tune PID loops.
We created this pocket guide to solve for simple solutions. If your needs are more complex, our team of field engineers and PhD’s would love to hear about it.
Questions? (440) 443-3900 | Send Us A Message
PID Loop Tuning Pocket Guide v6 Now Available
/in Press ReleasesWe have updated our PID Loop Tuning Pocket Guide! Version 6 includes information on integrating processes, how to test them when tuning open loops as well as the controller references for them too. By investing in tuning your PID loops (temperature, level, pressure and flow), your control loops will operate efficiently, rather than just being functional.
ControlSoft Releases INTUNE and INTUNE+ Software v6.6.0.0
/in Press ReleasesThe INTUNE and INTUNE+ Software, v.6.6.0.0 release, includes enhancements to the following areas:
For detailed information, please see the INTUNE Software v6.6.0.0 Release Notes, publication MN110A-EN, included with the software download.
ControlSoft Signs Value-added Reseller Agreement with Hiram Process Control Engineering
/in Press ReleasesControlSoft is pleased to announce the signing of a value-added reseller agreement with Hiram Process Control Engineering, a consulting company serving industrial process control companies in Israel.
Hiram Process Control is led by Avihu Hiram, a process and control expert with over 45 years of experience specializing in process control, process monitoring, process design and hazardous material safety, and focused on energy issues and environmental implications.
“We are pleased to welcome Hiram Process Control Engineering to the ControlSoft family,” said Tien-Li Chia, President at ControlSoft, Inc. “As we continue to expand our presence globally, Hiram Process Control Engineering will help us provide service to customers in Israel, and we look forward to a long and successful relationship.”
About ControlSoft
Since 1985, ControlSoft has been a global provider of platform-independent process control software and engineered solutions. Our products and services are sought by prominent companies in leading industries. By maintaining a focus on improving plant availability, production efficiency, operational safety and environmental compliance, we continue to deliver world-class control solutions for our customers.
Press contact
Paul Botzman
pbotzman@controlsoftinc.com
phone 440-443-3900, ext. 101
[This release was modified on May 6, 2020.]
PID Tuning Objectives and Considerations
/in Articles