PID Tuning Objectives and Considerations
The main objective in tuning PID controllers is to adjust the reactions of PID controllers to setpoint changes and unmeasured disturbances such that variability of control error is minimized. PID controllers are implemented primarily for the purpose of holding measured process value at a setpoint, or desired value.
Secondary objectives may exist and need to be considered when tuning PID controllers. Level controllers may not need to be tuned too aggressively to hold level exactly at a setpoint, for example at 50% of tank capacity. If the tank is installed to serve the purpose of a buffer in mass flow management between two process units the purpose of the control may be not to allow overflow or emptying the tank while keeping the tank outflow as steady as possible and keeping the level fluctuate within reasonable bounds around the target capacity.
When the actuator is a transformer or a control valve, tuning that ensures reasonable travel of the actuator may be desired to protect the actuator and provide for its maximum lifetime.
These tuning objectives are often conflicting and engineers must balance the importance of the objectives based on cost, i.e. solve an optimization problem. If a certain amount of PV deviation from the setpoint causes significantly increased cost to the manufacturer due to scrapped and downgraded product, this cost typically far outweighs wear and tear of the actuators. Then, solving the tuning optimization task yields a solution to tune the PID controller aggressively, minimize PV variability around the setpoint even though it causes the actuator to work hard, possibly requiring more frequent maintenance or replacements.
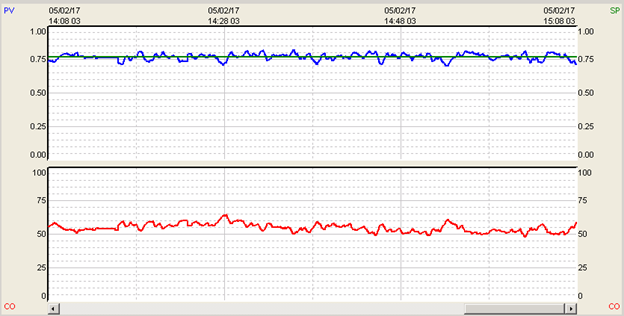
The tuning of the above process holds the process variable to setpoint with minimal variation above noise levels. Note that the valve has to move aggressively to achieve this result.
If higher PV variability around setpoint can be tolerated, in the sense that it does not increase cost of operation, then tuning can be slowed down to protect the actuator, i.e., conservative PID tuning can be applied. Such a situation may occur in tuning cooling air or cooling water circuits, when cooling media temperatures are well within operating ranges and aggressive control to exact cooling water temperature does not provide additional value.
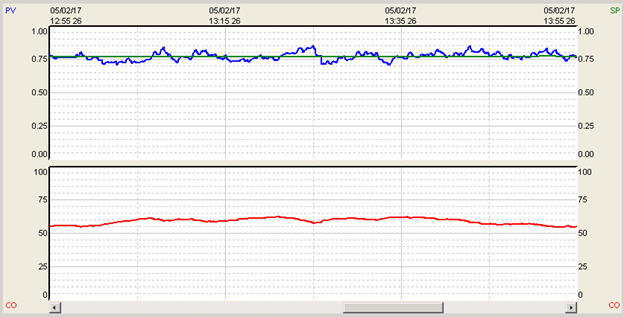
Tuned differently, the same process does not hold the process variable to setpoint as well and there is more variability in the product from the desired setpoint. This will likely affect quality and/or cost of the product. Note that the valve movement is much smoother with this tuning and will likely result in less maintenance cost and less wear on the process hardware.
A combination of conservative and aggressive tuning may be applied during the above mentioned level control. To stabilize flow out of the tank, conservative tuning can be applied when the tank level is in the predefined range. When a condition occurs that the tank experiences higher or lower than usual inflow, the mass balance must be satisfied and an aggressive control action applied to prevent tank overflow or emptying. In such a case, the objective of stable outflow is sacrificed or given up on to prevent violating tank level limits.
During a unit’s first startup, engineers apply default tuning parameters. These parameters may be copied over from similar units commissioned before, or very slow conservative parameters to avoid initial instability, or parameters favoring Integral action to provide for smooth controller output, or simply default parameters provided by the DCS/PLC vendor. The goal of the initial PID tuning parameters is to provide for some level of safe functioning of the process unit to get the unit started up and then later during commissioning, properly tune the PID controllers.
Then, an engineer is assigned the task to tune the PID controllers. If tuning software is used or if a specific tuning method is used, then in the tuning of multiple PID parameters a pattern of tuning can be observed. However, if the engineer proceeds with a trial and error method then the engineer’s subjective preferences play a significant role.
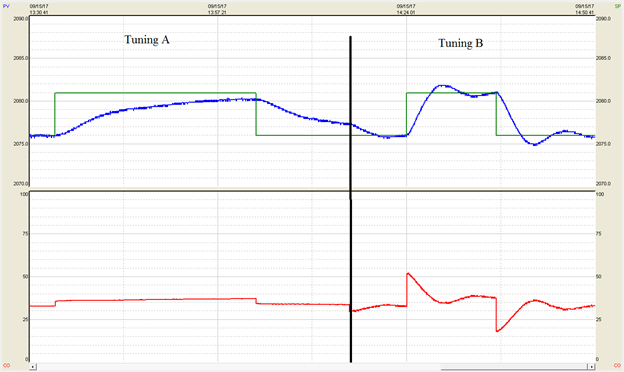
Above we show response results for two different PID tuning parameters. Tuning A is slow, and takes a long time to reach setpoint. Tuning B gets to setpoint relatively quickly, but has some resultant overshoot in the Process Variable. If the process cannot tolerate overshoot from the setpoint by more than 1-2 EU, then tuning A would be the desired tuning. This would reduce the chance that product is scrapped when the SP is exceeded. If overshoot in the process can be tolerated, tuning B would be more desired. Since we reach setpoint sooner, more product can be produced over time.
Engineers with process background tend to favor the process objectives, i.e. tuning to hold PVs closely to the setpoints, favoring proportional action. Electrical engineers, responsible for the automation infrastructure, may tend to protect the infrastructure and tune more conservatively, favoring the integral action. Intuitively the two groups in this example favor one tuning objective over another.
Tuning based on subjective preferences should be avoided even though it may provide for stable and robust operation of the PID controllers. PID controllers make important decisions on control outputs every second and if these decisions are not optimal with respect to the actual cost of manufacturing, the tuning will yield suboptimal overall plant results.
Extremely slowly tuned PID controllers can be considered operating in almost manual mode, not moving the control output much even though frequent or permanent disturbances are present.
Extremely aggressively tuned PID controllers may be operating very close to instability. Rejecting disturbances very aggressively, holding PV at setpoint very tightly, often experiencing low magnitude constant oscillation around setpoint that may be difficult to notice e.g. due to some measurement noise. Then, if a setpoint change is made or operating conditions change slightly, an aggressively tuned controller may start to oscillate dramatically or even saturate at maximum and minimum control output repeatedly.
PID control tuning is an engineering task where operational and economic objectives should be weighed and analytical methods should be used to determine a viable range of P and I settings and robustness of performance should be verified over a period of time after the tuning was last changed. This approach will yield close-to-optimal tuning based on operational objectives and ensure safe operation at minimal production cost.
For more helpful information on how to tune PID controllers, request a free copy of our PID Loop Tuning Pocket Guide.